Artykuł sponsorowany
Budowa maszyn na zlecenie – od koncepcji do gotowego rozwiązania
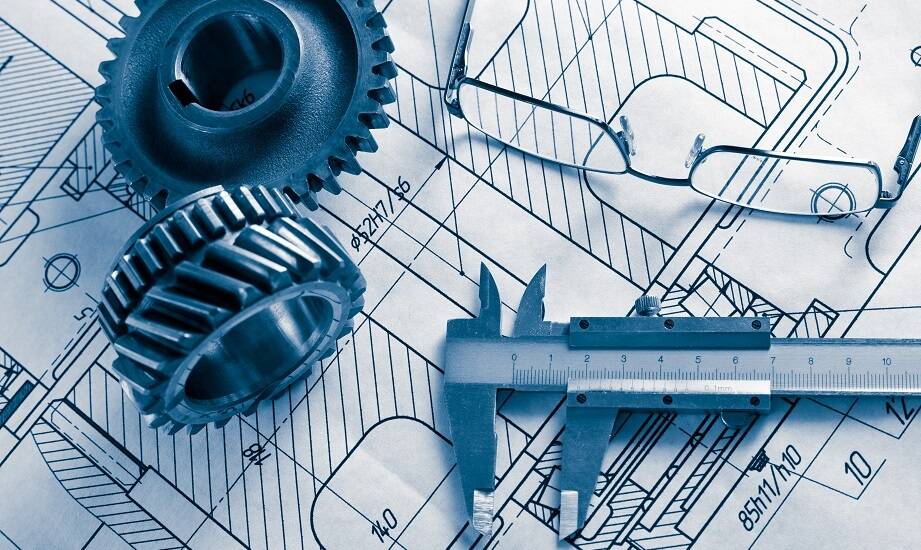
Budowa maszyn na zlecenie odgrywa kluczową rolę w przemyśle, gdzie standardowe rozwiązania często nie spełniają oczekiwań. Dostosowane projekty przynoszą liczne korzyści, takie jak zwiększenie efektywności produkcji czy redukcja kosztów. Proces tworzenia maszyn obejmuje kilka etapów, począwszy od analizy potrzeb klienta aż po wdrożenie gotowego rozwiązania. W dalszej części artykułu przedstawione zostaną poszczególne etapy budowy, ich zastosowania oraz przykłady udanych realizacji i aktualne trendy w naszej dziedzinie.
Etap koncepcyjny i analiza wymagań
Na początku procesu budowy maszyn na zlecenie kluczowe jest zrozumienie potrzeb klienta oraz specyfiki branży, w której będzie działać urządzenie. W tym celu przeprowadza się różne metody zbierania wymagań, takie jak wywiady, ankiety czy warsztaty. Następnie dokonuje się analizy funkcjonalnej, która pozwala określić główne cele i zadania maszyny. Wstępne szkice i modele pomagają zwizualizować koncepcję oraz ocenić jej wykonalność.
Współpraca z klientem ma ogromne znaczenie – regularne konsultacje umożliwiają wprowadzanie zmian oraz dostosowanie projektu do oczekiwań. Etap koncepcyjny stanowi fundament dalszych prac, dlatego warto poświęcić mu odpowiednią uwagę. Dobrze przeprowadzona analiza wymagań przekłada się na efektywność i jakość końcowego rozwiązania, co z kolei wpływa na satysfakcję klienta oraz sukces przedsięwzięcia.
Projektowanie maszyn i prototypowanie
Projektowanie maszyn i prototypowanie rozpoczyna się od analizy wymagań klienta, co prowadzi do stworzenia szczegółowych rysunków technicznych oraz specyfikacji materiałowych. W tym etapie wykorzystywane są zaawansowane narzędzia i technologie, takie jak CAD (Computer-Aided Design), które umożliwiają precyzyjne modelowanie 3D oraz symulacje działania urządzenia. Prototypowanie odgrywa kluczową rolę w weryfikacji rozwiązań projektowych – pozwala na ocenę funkcjonalności, wydajności oraz ergonomii przed rozpoczęciem produkcji seryjnej. Dzięki temu możliwe jest wprowadzenie ewentualnych poprawek i optymalizacja konstrukcji, co przekłada się na lepszą jakość końcowego produktu oraz zadowolenie klientów. Proces ten jest niezbędny dla osiągnięcia wysokiej efektywności i niezawodności maszyn, a także minimalizacji ryzyka awarii oraz kosztów eksploatacji w późniejszym etapie użytkowania.
Produkcja i wdrożenie gotowych rozwiązań
Etap produkcji rozpoczyna się od wyboru odpowiednich materiałów i technologii wytwarzania. Kluczowe jest również zapewnienie kontroli jakości na każdym etapie procesu. Logistyka oraz terminowość dostaw mają ogromne znaczenie, aby klienci otrzymali gotowe rozwiązanie w ustalonym czasie. Po zakończeniu produkcji następuje proces uruchamiania maszyn, który często wymaga wsparcia specjalistów z firmy budującej urządzenie. Ważne jest także posprzedażowe wsparcie, które może obejmować serwisowanie czy dostarczanie części zamiennych. Dzięki temu klienci mogą być pewni, że zakupione maszyny będą działały sprawnie przez długi czas, a ewentualne problemy zostaną szybko rozwiązane.